Manufacturing - Industry 4.0
Enabling faster innovation.
Manufacturers' outlook for the future
Technology inventions are fueling momentous change in the manufacturing industry at large. However, these changes aren't occurring in a vacuum. Increasing digitised processes Industry 4.0 is the convergence of top-level and shop-floor systems, manufacturing and business processes.
Manufacturing is moving away from appliances to consolidated, disaggregated and integrated workloads. This transition makes better use of data to improve decision-making, planning, productivity, safety, quality, and other business aspects.
Data, represents a way of unlocking knowledge traditionally trapped within your production floor. Gaining access to this information by connecting assets in a secure way via edge, distributed core, or cloud computing allows previously untapped data to become used within a business and drive more informed decision-making. Patrica Florissi, CTO, Dell EMC
Here are the top five trends:
1. Global competition is fierce
The shifting geopolitical landscape is prompting governments in some parts of the world to become more stridently nationalistic. For example, the new tariffs currently being pursued by the US and the UK’s withdrawal from the EU are both generating trade friction. Big decisions need to be made on how to fund critical investments such as plant relocation. Over half (55%) of manufacturing CEOs believe a return to territorialism poses the greatest threat to their operations – way ahead of cyber security risks (37%) - Global Manufacturing Outlook data from 2018 Global CEO Outlook, KPMG International.
2. Manufacturing is no longer just making things
The trend for increased personalisation and customisation is here to stay and demands that factories shift from the ‘make to stock’ approach in favour of ‘make to order’, ‘engineer-to order’ or ‘configure-to-order'. Hyper-specialised and heavily automated small factories are posing a growing threat to established businesses, particularly with the advent of additive manufacturing which is accelerating new business model innovation. So rather than being ‘all things to all people’, connected factories are increasingly distributing risk and capital expenditure among the various parties involved to allow them to focus on their respective strengths. Supply chain leaders are focusing on three key priorities:
- The use of digital connections with customers to better understand and drive the Total Customer Experience.
- Digital automation and augmentation of supply chain capabilities.
- A shift towards a lifecycle-based approach to understanding the total impact of products and operations across the value chain. -The Gartner Supply Chain Top 25 for 2018
3. Servitization is becoming a common strategy
In its simplest terms, servitization refers to industries using their products to sell “outcome as a service” rather than a one-off sale. More and more businesses that have historically sold products are now selling capabilities, services and outcomes in an attempt to future-proof themselves against commoditization. ‘Servitization’ is essentially about moving from a product-centric to a service-centric model. The main aim is to develop longer-term relationships with customers rather than one-off transactions, with a secondary motive to create recurring, profitable revenue streams. Take Formula 1 constructor, McLaren, which is applying its expertise in electronic systems, telemetry, software, sensor technology, simulation and predictive analytics to industries beyond motorsport. However, servitization calls for a new set of capabilities, from providing consumables to condition monitoring, repairs, maintenance and end-of-life product disposal. Forward-thinking manufacturers, therefore, need both the strategy and the resources – people, materials, finances and systems – in place if they are to deliver such value-added services and solutions.
4. The financial outlook is cautious
Manufacturers’ big-ticket decisions continue to be influenced by the availability of bank financing, cash reserves on the balance sheet, and the measure of confidence within the sector to invest in digital technologies. A healthy supply of low-cost labour has given some businesses an excuse not to place their bets on long-term profitability through investment, preferring to sweat fixed assets and focus on the short-term profits. However, most manufacturers (87%) really do want to invest in new plants and ‘Industry 4.0’ technology to boost productivity. Digitisation is, therefore, key to product and process development. Given the relatively complex nature of digital transformation projects, traditional financing partners may not be the best choice to support these initiatives. Instead, organisations should look to companies that have a broad and deep understanding of not only the technologies themselves, but also the processes involved, and the path to value over time. For companies that want to keep their IT investment up and running longer, beyond the scope of the manufacturer support timeline we can help with our IT Support and Maintenance Services.
5. The sector is facing a skills shortage
Increasing digitisation, interconnection and automation is often associated with potential job losses – a belief that has led some manufacturers to defer investment in technology to avoid workplace unrest and maintain wider social harmony. Nevertheless, competitiveness is still the most effective way to create and keep jobs over the longer term, and more enlightened businesses are acknowledging that automation will not necessarily eliminate jobs but instead redefine them. In reality, the rapid adoption of advancing technologies, coupled with an ageing workforce, is contributing to an overall industry shortage of workers with STEM (science, technology, engineering and mathematics) skills.
Unless immediate action is taken, experts including Deloitte and the Manufacturing Institute warn that by 2025, there will be a potential shortfall of two million skilled manufacturing workers in the US alone.* Due to poor, albeit outdated, public perception of the sector, manufacturers are currently facing a digital talent gap and difficulty in attracting millennial brainpower. For example, data scientists are hot commodity across every industry, so manufacturers who are already facing intense competition from high-profile, high-tech companies for the best and brightest. There is an urgent imperative for both the industry and academia to reposition manufacturing to the upcoming, tech-savvy generation as a dynamic, innovative environment with rich and rewarding career prospects. Other options include IT Support to allow access to certified experienced IT engineers that become an extension of your team.
Source: Dell Technologies, The evolving manufacturing outlook.
92% of manufacturers believe Smart Factory technologies will enable them to increase productivity levels per headcount 92% Annual Manufacturing Report 2018, The Manufacturer.
Manufacturers are sitting on mountains of data that, with the right technology investments and digital transformation strategy, can be exploited and interconnected to create new, agile and disruptive business models. To advance operational excellence by allowing decision-makers – whether human or machine – to spot system weaknesses before they become problems. Data will also improve the transparency of increasingly complex global supply chains. Insights will also aid design and develop better products and services that align with customers’ needs and preferences.
Operational improvements to address the traditional goals of “cheaper, better, faster” throughout the value chain, from concept to delivery |
Customer experience data-driven initiatives that provide a personalized experience to the customer for both products and services. |
Product innovation is informed by integrating data across the product lifecycle and ecosystem, to improve the design and performance of existing products and create new ones. |
New business models by identifying servitization opportunities within your existing portfolio enabled by the connected ecosystem |
Primenet with our Partner Dell Technologies is here to help our customers embrace the digital future, unlock new capabilities, and seize the opportunity available.
To talk to our team of experts, we are available 24/7 365 days a year. Whether you require Maintenance & IT Support, to gain immediate value by implementing selected hardware or you require a cyber assessment.
Related Topics
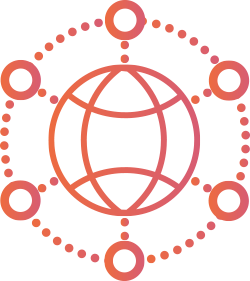
Internet of Things